Il monitoraggio dei cambiamenti nella produzione - avanzamento, tempi di consegna, possibili fonti di ritardo - svolge un ruolo particolarmente importante nel settore. La consegna tempestiva dei prodotti è spesso determinata da diversi fattori: tempi di inattività, tempi di produzione e stabilità del processo produttivo. Inoltre, i rapporti cartacei vengono spesso consegnati con ritardi di molte ore, prolungando così i tempi di reazione. Questo potrebbe essere evitato con la digitalizzazione.
Gli ordini non consegnati in tempo e secondo gli accordi con l’appaltatore rappresentano un problema comune per le aziende del settore industriale, a causa delle elevate sanzioni finanziarie contrattuali. Ciò interrompe la catena di fornitura, spesso porta a controversie finanziarie e disturba il funzionamento generale dell’azienda manifatturiera, con ripercussioni sull’intero piano di produzione e ulteriori ritardi. Per questo motivo è importante lavorare secondo un programma prestabilito e ridurre al minimo tutti i fattori che possono influire sulla puntualità dell’esecuzione degli ordini, oltre a valutare e comunicare in modo efficiente quali ordini di produzione sono o possono essere a rischio.
L'efficienza della produzione industriale è talvolta influenzata da tempi di inattività non pianificati, che hanno un impatto sui KPI. Tuttavia, la gamma dei possibili problemi è molto più ampia. Questi includono:
- fermi di produzione non programmati,
- carenze di materiali - carenze di materie prime e altri componenti,
- rallentamento del ciclo produttivo,
- qualità inadeguata degli elementi fabbricati,
- tempo eccessivo per la sostituzione,
- tempi prolungati per l'avvio della produzione.
È inoltre evidente che tra i fattori che stanno diventando più gravi c'è la mancanza di ripetibilità nel processo di produzione. Ciò influisce negativamente sulla capacità di prevedere il completamento di un ordine di produzione, con conseguenti ripercussioni sull'efficienza produttiva.
Tempo vs monitoraggio dell'avanzamento della produzione
La ricerca delle cause dei problemi deve essere effettuata il prima possibile. Se si implementa il monitoraggio della produzione in tempo reale, è possibile evitare i rapporti cartacei e i ritardi di fine turno. Inoltre, l’analisi dei dati su un periodo di tempo più lungo sarà facile e accurata e garantirà una risposta rapida agli errori.
Il monitoraggio della produzione in tempo reale può essere effettuato da MES. L’automazione della produzione e la generazione di report basati sui dati correnti influenzano la velocità con cui vengono prese le decisioni di ottimizzazione. Il ruolo significativo del MES è quello di fornire dati sulla produzione relativi allo stato, alla produttività e ai motivi per cui la produzione non è puntuale. A tal fine, il sistema deve essere integrato con i dati provenienti direttamente dalle macchine.
Un importante vantaggio di tale soluzione è anche la certezza della loro accuratezza. Si può ritenere che la raccolta automatica dei dati dai dispositivi mediante un software di tracciamento della produzione sia oggi il metodo più affidabile per ottenere dati in tempo reale.
Raccolta di dati da macchine nuove e preesistenti
Contrariamente alle preoccupazioni diffuse, l’età delle macchine e le modalità di controllo non devono essere un ostacolo quando si tratta di raccolta automatica dei dati. In pratica, con le attuali capacità tecnologiche, la connettività delle macchine è disponibile per qualsiasi tipo di macchina di produzione. Questa versatilità è dovuta all’utilizzo di numerosi formati di comunicazione.
Se la macchina è dotata di un PLC, si collega ad esso direttamente o tramite convertitore. Ciò avviene tramite i protocolli standard TCP e PLC nativi (OPC DA/UA, Siemens, Allen Bradley, Beckhoff, B&R, Omron, Mitsubishi, GE Fanuc).
Nel caso in cui la macchina non disponga del PLC, o sia impossibile ottenere i dati in modo semplice ed economico, leggiamo i dati dal livello di automazione mediante la duplicazione dei segnali.
La lettura completa dei dati del livello di automazione comprende tutti gli indicatori importanti e sensibili. Questi includono:
- contatori di produzione,
- stato della macchina,
- parametri di processo (ad esempio, velocità, pressione, temperatura, angolo, dimensioni),
- raccolta automatica di informazioni sulle cause e sulla durata dei tempi di inattività,
- segnalazione di micro-arresti grazie alla profonda integrazione con i controllori PLC.
Vale la pena notare che anche una semplice informazione, ad esempio che una macchina sta funzionando o meno, può innescare il monitoraggio dell'avanzamento della produzione, aumentando la correttezza, l'affidabilità dei dati e, soprattutto, il tempo. Grazie a questo sistema, possiamo monitorare automaticamente fino a 5 parametri:
- il tempo di ciclo effettivo della macchina,
- il numero di cicli,
- il tempo di funzionamento della macchina,
- i tempi di fermo macchina,
- micro-stop.
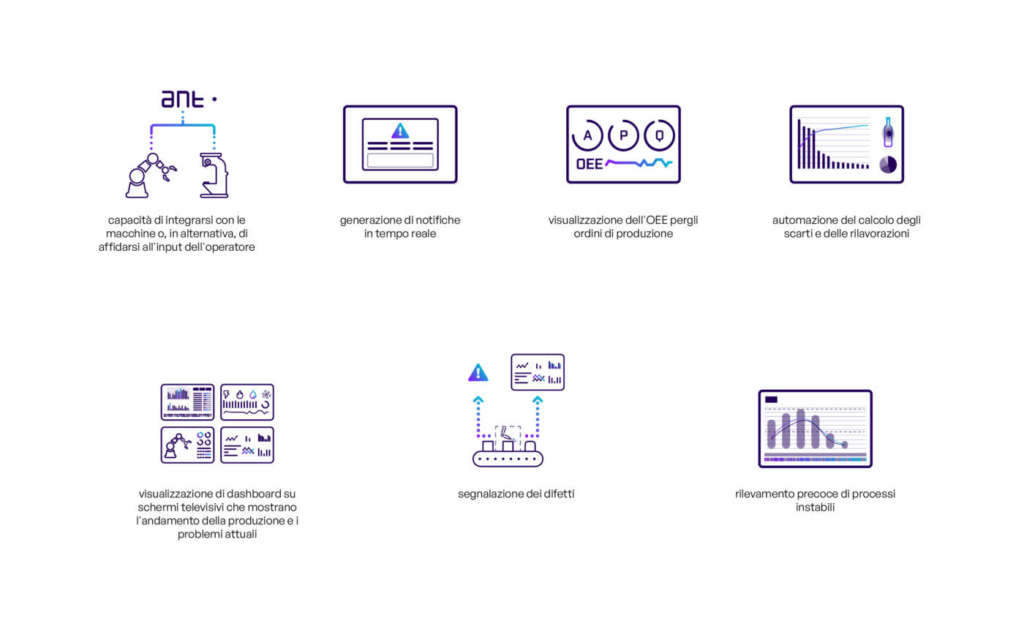
Il ruolo dell'operatore nel contesto del monitoraggio della produzione
Se il processo è manuale o la macchina non è in grado di fornire tutte le informazioni, dobbiamo affidarci all'operatore. Include:
- avviare la produzione in sequenze pianificate e sempre aggiornate,
- segnalazione - se necessario - dei volumi di dati all'interno delle voci OK/NOK,
- monitorare l'avanzamento della produzione, gli stati delle macchine e i ritardi di produzione,
- Controllo di qualità.
L’operatore può anche estendere la portata delle informazioni raccolte automaticamente. Ad esempio, può visualizzare i motivi dei tempi di fermo, i codici di errore e di guasto insoliti e qualsiasi altro dato necessario per un’analisi approfondita.
Utilizzo del modulo di esecuzione della produzione ANT in produzione
L’utilizzo del modulo di esecuzione della produzione ANT implica principalmente l’integrazione bidirezionale dei sistemi utilizzati in azienda. Ad esempio, ERP, APS e WMS. In questo modo è possibile eliminare le doppie relazioni e accelerare il flusso di informazioni. I dati così raccolti possono essere utilizzati per visualizzare in tempo reale piani di produzione, KPI, ritardi di produzione registrati.
Un altro importante vantaggio del modulo è la possibilità di raccogliere informazioni sullo stato di ogni macchina e sulla realizzazione del piano di qualità e produzione. Il sistema aiuta ad analizzare le cause dei ritardi negli ordini di produzione. Altre possibilità sono:
- la capacità di integrarsi con le macchine o, in alternativa, di affidarsi ai dati inseriti dall'operatore,
- la generazione di notifiche in tempo reale,
- la visualizzazione di OEE per gli ordini di produzione,
- automazione del calcolo degli scarti e delle rilavorazioni,
- visualizzazione di dashboard su schermi televisivi che mostrano l'andamento della produzione e i problemi attuali,
- segnalazione dei difetti,
- rilevamento di processi instabili in una fase iniziale.
Quali sono i vantaggi del monitoraggio dei progressi della produzione?
Il vantaggio principale dei sistemi di monitoraggio dell’avanzamento della produzione è quello di aumentare il volume della produzione e la trasparenza dei processi industriali. Effetti chiaramente visibili sono anche i risparmi di materiale derivanti dalla riduzione degli sprechi.
L’analisi continua della produzione per mezzo di un sistema di tracciamento della produzione porta anche a tempi di risposta più brevi per l’eliminazione dei guasti. Fattori importanti per l’efficienza del processo sono anche:
- facile localizzazione e valutazione del rischio di mancata esecuzione di un ordine di produzione,
- supporto nella realizzazione del piano di qualità e produzione,
- decisioni basate su dati e notifiche in tempo reale,
- monitoraggio dei livelli attuali di scorte su una macchina,
- migliorare significativamente l'accuratezza della programmazione,
- analisi delle prestazioni effettive delle vostre macchine.
Pertanto, l’implementazione di un software di monitoraggio dell’avanzamento della produzione porta a una valutazione molto migliore e più completa delle condizioni generali della fabbrica. Indipendentemente dal settore, il sistema di monitoraggio dell’avanzamento della produzione è in grado di fornire un feedback completo su quale macchina sia più adatta a produrre un particolare articolo. Anche la capacità di calcolare i tempi di ciclo effettivi per i singoli componenti e le macchine ha un impatto sulle prestazioni.